传统工程软件已过时?EPLAN如何重构机电一体化未来?
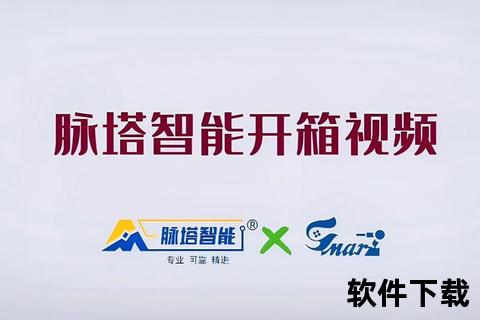
当全球制造业面临产品复杂度飙升、交付周期压缩的挑战时,一个争议性问题浮出水面:传统CAD软件割裂机械与电气设计的模式,是否已成为制约工业4.0发展的瓶颈?某机床企业曾因机械与电气团队使用不同软件,导致设备调试时出现137处接口错误,直接损失超300万元。这场“协同灾难”印证了市场对新型工程平台的需求,而德国EPLAN软件以55000家企业用户的实践,给出了智能化破局方案。
1. 跨学科协同难题如何破解?
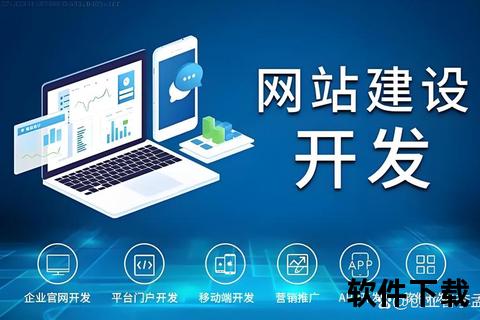
在船舶制造领域,某企业设计的自动化控制系统涉及2.6万条线缆、8000个端子,传统ECAD软件需要3个月才能完成原理图与三维布线的数据同步。引入EPLAN Platform后,通过Electric P8与Pro Panel的深度集成,机械工程师的3D机柜模型可实时关联电气原理图,布线错误率降低78%,设计周期缩短至45天。
更典型的案例是中冶赛迪为钢铁厂设计的低压配电系统。项目初期使用EPLAN Preplanning进行全局规划,将设备参数、线缆规格等数据存入中央数据库。当某型号断路器因供应链问题需要替换时,系统自动更新了12套相关图纸和采购清单,避免传统模式下需手动修改200多个文件的繁琐操作。
2. 云端协同真能突破地域限制?
某新能源汽车企业在德国、上海、墨西哥三地同步开发充电桩时,曾因版本混乱导致工程延误。通过EPLAN Cogineer Advanced的云端部署,设计团队利用Microsoft Azure平台实现实时数据共享。当德方修改某个接触器参数时,系统自动触发中国团队的线径计算模块更新,墨西哥工厂的安装指导手册同步生成二维码。这种“数据动车组”模式使项目交付速度提升40%,异地协同成本下降65%。
台达电子在智慧工厂项目中更展现出云端优势。工程师通过EPLAN Cloud直接调用施耐德、西门子等厂商的3D模型库,在移动端完成90%的电气柜布局设计。现场安装时,AR眼镜读取设备二维码即可调取最新图纸,较传统纸质文档查找效率提升5倍。
3. 智能化工具如何重构设计逻辑?
苏州某机器人企业曾因人工布线效率低下,月产能卡在200台瓶颈。应用EPLAN Smart Wiring 2.8后,软件通过机器学习分析历史项目数据,自动优化线缆路径。对于重复率超过85%的控制柜布线,系统生成标准化方案库,使单个机柜布线时间从8小时缩短至1.5小时,错误率趋近于零。
更革命性的改变来自EPLAN 2025的预测性分析功能。某电力设备厂商在设计海上风电变流器时,Pro Panel的故障模拟模块提前识别出盐雾环境可能引发的16处绝缘问题。通过虚拟环境加载热带风暴参数,系统自动调整元器件布局方案,使产品现场故障率下降92%。
走向智能工程的实践路线图
对于寻求转型的企业,建议分三阶段实施:
1. 基础建设期(6-12个月):优先部署EPLAN Electric P8与Data Portal,建立标准化元件库。参考青岛软控经验,初期投入可使设计效率提升50%
2. 系统集成期(12-24个月):引入Pro Panel与Preplanning,打通机械、电气数据流。如航天云网通过平台整合,将工程变更响应速度提升至4小时
3. 智能升级期(24+个月):对接企业ERP与MES系统,部署云端协同与AI模块。某德资企业在此阶段实现设计错误趋零化,项目利润率提高19%
高效赋能EPLAN软件开启智能工程新时代,不仅是工具革新,更是工程思维的进化。当中国制造2025遇上工业4.0,这个深度融合机电软一体化、云端协同与智能预测的平台,正在重塑从图纸到产品的每个比特与原子。正如德国Smart Factory KL实验室展示的,未来工厂的竞争力,始于今日工程数据流的精准与灵动。